Foundation for paperless production: Fischer Group digitalizes shopfloor processes with ORBIS MES
Sectors: Manufacturing industry, Steel / Steel Service Center / Metal industry, Mechanical and plant engineering
Processes: Manufacturing
References: F. E. R. Fischer Edelstahlrohre GmbH
With the introduction of the ORBIS Manufacturing Execution System (ORBIS MES), Fischer Group is increasing its degree of digitalization and thereby improving efficiency and transparency in production. At the same time, the company is laying the foundation for sustainably optimizing its shopfloor processes and implementing paperless production.
Sector: Metal and steel processing
Production sites: Achern-Fautenbach (head office)
Products: Longitudinally welded stainless steel tubes, components and assemblies made of stainless steel tubes, special solutions for industrial applications
Employees: Approx. 2,700
Website: www.fischer-group.com
The company placed its trust in ORBIS SE’s expertise to implement and expand ORBIS MES.
Durable, corrosion-resistant and temperature-resistant tubes that can withstand extreme stresses ensure the smooth and safe operation of exhaust and fuel systems in vehicles, oil and gas supply systems and power plants, while also guaranteeing continuous water treatment and drinking water supply at all times.
The market leader for longitudinally welded tubes
One thing that most people don’t realize is that these tubes often come from the Fischer Group’s Achern-Fautenbach site in Baden-Württemberg. Founded in 1969, this family-run company ranks among the leading manufacturers of longitudinally welded tubes made of stainless steel, titanium and nickel-based alloys.
At sites spread across eight countries worldwide, around 2,700 employees process over 162,000 metric tons of steel into more than 127 million meters of tubing every year. It is further processed into components and assemblies or molded into complex 3D shapes by means of hydroforming.
Source Photo: F. E. R. Fischer Edelstahlrohre GmbH
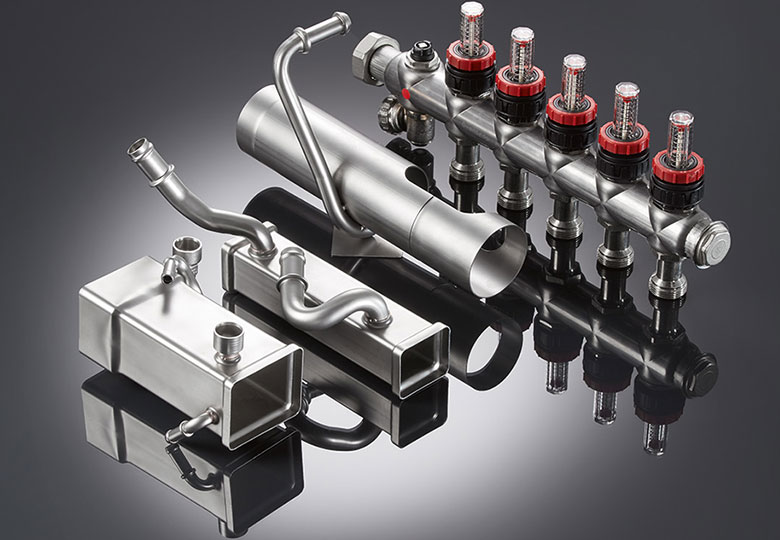
But the medium-sized company doesn’t just owe its economic success to its high-quality products. This is also due to its continuous innovation, highly motivated workforce and tremendous depth of value creation. All the services come from a single source – from tube production to semi-automated installation of assemblies – and products are manufactured using internally developed machines and tools.
Modernizing IT with SAP S/4HANA and ORBIS MES
If the Fischer Group is to continue operating successfully and growing on the market, it is absolutely essential that it increases its degree of digitalization by comprehensively modernizing its IT facilities to standardize its business processes, increase their transparency and achieve sustainable optimization. An important step in this direction has already been taken by simultaneously introducing and commissioning SAP S/4HANA Cloud and ORBIS MES. The ORBIS Manufacturing Execution System integrates seamlessly into SAP’s ERP suite, which was implemented using the greenfield approach with the help of RISE with SAP.
The simultaneous go-live was necessary because Fischer’s intention was to use the MES from the SAP S/4HANA go-live to map the shopfloor processes and record production data (PDA). End users record production data such as quantities, weight, unit numbers, work progress, order status and personnel data (including attendance / absence times, working hours, wage costs and access control).
The vision: paperless production
„ORBIS MES provides us with very efficient support in digitalizing and improving production processes, not to mention networking and standardizing them across sites. By doing this, we are laying the foundation for turning our long-term vision of paperless production into a reality.“
Thorsten Obert (Head of Information Technology at F. E. R. Fischer Edelstahlrohre GmbH)
The stainless steel tubes and components manufacturer is already benefiting significantly from ORBIS MES. It can seamlessly track incoming and outgoing batches throughout the entire production process and across several production stages. Consumption is posted with a high level of accuracy. Thanks to digital actual-time recording, the target / actual comparison of production-relevant times has also improved significantly. The end users (there are 550 at present) also appreciate the solution’s user-friendly user interface, which reliably guides them through the individual process steps, speeding up processes and preventing input errors.
Seamless integration with QM and embedded EWM
The Fischer Group is particularly benefiting from the bidirectional integration between ORBIS MES and quality management, not to mention embedded EWM in SAP S/4HANA.
While SAP Quality Management (SAP QM) transmits inspection specifications to the MES, ORBIS MES controls when and to what extent the inspections are due and actively alerts users. Measurement results are either manually recorded by means of PDA or transferred from the various measuring devices using Steinwald boxes at the push of a button. What’s more, the results of complete inspection sequences from measuring machines are transferred over a file interface (Q-DAS transfer format) to the MES, which automatically evaluates and displays them. All the measurement and inspection results collected in ORBIS MES are promptly transferred to SAP QM, where they are available for evaluations or inspection certificates.
The embedded EWM, in turn, provides information about packaging specifications for the materials to be produced in ORBIS MES during goods receipt posting. The handling units (including nested ones) are then generated in ORBIS MES. Conversely, information about production orders and workstations that is required for transfer postings and printing and was previously recorded in ORBIS MES by means of PDA is incorporated into SAP EWM.
Tight schedule and budget met
Ultimately, this seamless integration and the smooth data exchange between ORBIS MES and SAP S/4HANA’s intralogistics and quality management applications were the deciding factors in the customer choosing this production solution.
The MES implementation process was completed within the tight schedule and the allocated budget. This success can be attributed to the collaborative and goal-focused partnership between internal key users and specialist departments, plus the ORBIS consultants. Thanks to effective teamwork, MES was adjusted to the Fischer Group’s process requirements on schedule.
Mapping individual process requirements
Among other things, the company required the integration of a document management system and various process alignments and simplifications through special posting and calculation logics. For example, what is known as the “primary setup” of a production line during its conversion to a new product is mapped in the MES through setup orders as a special order type.
It was also necessary to be able to enable bundling of related material call-offs for individual production orders uniformly under a single sequence number. Additionally, MES users can now also use a collective order to record times for activities performed for other plants. Status changes within a production order are also inherited not only on the first operation, but also on subsequent operations by means of defined control characters.
Machine connection and rollout planned
Mr. Obert summed up the experience positively:
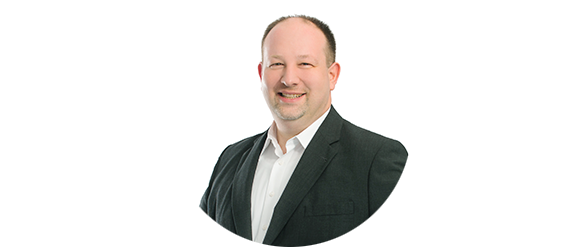
„With the implementation of ORBIS MES, the degree of digitalization in shopfloor processes, and consequently efficiency and transparency, have increased significantly. We are benefiting from numerous improvements and simplifications. We will now consistently continue along our chosen path.“
Thorsten Obert (Head of Information Technology at F. E. R. Fischer Edelstahlrohre GmbH)
A pilot project for automatically logging up-to-date machine data (MDL) is currently being carried out on a selected system. This is another important step towards digitalizing and optimizing production processes, as the collected data is directly available for analyses. There are also plans to roll out ORBIS MES, which is currently being used in the Achern plants, to all the production sites worldwide with a view to establishing standardized shopfloor processes across all plants.