NETZSCH launches standardized, interoperable shop floor platform using ORBIS DSP, SAP and Microsoft cloud solutions
Sectors: Manufacturing industry, Mechanical and plant engineering
Processes: Intralogistics, Warehouse control, Manufacturing
References: NETZSCH
The NETZSCH Group plans to secure its future success through its digitalization strategy. A key element of this is the implementation of fully digitalized processes in Production. The Pumps & Systems business area has paved the way for this with a future-oriented, standardized, and interoperable shop floor platform that combines SAP and ORBIS MES applications with Microsoft Azure Cloud. At its core is the ORBIS Distributed Shopfloor Processing (ORBIS DSP) solution, which interoperates with all applications.
Sector: Mechanical engineering
Headquarter: Waldkraiburg in Oberbayern
Products: Rotary positive displacement pumps from screw pumps, rotary lobe pumps and progressive cavity pumps to peristaltic pumps, including associated digital services
Employees: more than 4,000 (2022; NETZSCH Group)
Website: www.netzsch.com
Pretty much nothing moves without rotary positive displacement pumps – this is true for the oil and gas industries, the environmental and energy sectors, the food, pharmaceutical, chemical and paper industries as well as for mining. The pumps are used for wastewater treatment, for the conveying of oil and gas, lubricating and hydraulic oils, sewage sludge, explosives, highly viscous substances, substances containing solids, and also for unloading crude oil.
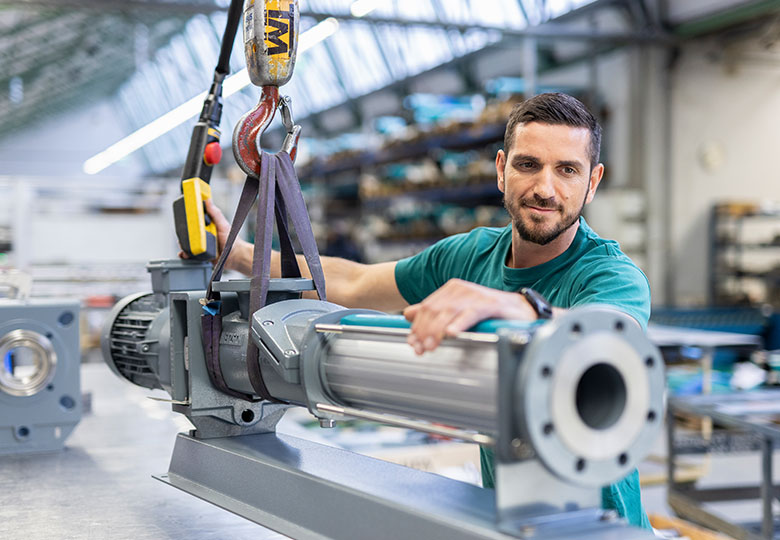
Leading specialist for positive displacement pumps
NETZSCH Pumpen & Systeme GmbH is a leading specialist in the development and manufacture of these pumps. Based in Waldkraiburg in Upper Bavaria, the company manufactures around 60,000 such units per year, including everything from screw pumps, rotary lobe pumps and progressing cavity pumps to peristaltic pumps, tailored to specific customer requirements.
Source Photo: © Netzsch
NETZSCH Pumpen & Systeme is part of the NETZSCH Group, which is also active in the areas of Analyzing & Testing and Grinding & Dispersing and employs over 4,000 people in 210 sales and production centers across 35 countries. Combined under the umbrella of a holding company, the individual units operate as independent entities to offer each customer the best possible solution. The company is committed to ongoing innovation, outstanding performance in all areas ("Proven Excellence" is its claim) and digital services in order to maintain and expand its leading market position and increase business value.
Shop floor digitalization with an interoperable platform
But key factors for continued market success also include the digitalization, standardization and sustainable optimization of processes in Production and at business management level. The pump manufacturer had already laid the foundation for this in terms of commercial processes by converting to the SAP S/4HANA platform, on which the existing ORBIS MES can also be used. This means that the prerequisites for the introduction of a modern, future-proof, standardized, scalable and, above all, interoperable shop floor platform, which can be used at production locations worldwide, were already established in Production and Logistics.
“The development and implementation of this platform was an important strategic step. It allowed us to establish digital, paperless, and interoperable shop floor processes in one place, covering everything from maintaining parameters for production specifications, order processing and machine control through to reporting on key production figures,” says Andreas Freiberger, SAP Inhouse Consultant at NETZSCH.
The new platform from ORBIS replaces a locally installed proprietary legacy solution for ME and QM processes, parameter maintenance and reporting, which couldn't be connected directly to SAP ERP (SAP S/4HANA or previously SAP ERP) and whose support is not guaranteed as it is no longer being updated.
ORBIS DSP ensures interoperability
The shop floor platform combines on-premises and public cloud solutions: the SAP-based ORBIS Manufacturing Execution System (ORBIS MES), which integrates seamlessly with SAP S/4HANA and was already in use in some areas of stator production, with a low-code Microsoft Power Platform-based app for creating and managing production specifications and the Azure IoT platform. Process data from the machines is stored there and analyzed using Microsoft Power BI.
The ORBIS Distributed Shopfloor Processing (ORBIS DSP) solution, a functional extension that ensures interoperability, i.e. the smooth interaction of the individual applications, is at the core of this platform. The innovative application from ORBIS SE consists of a self-contained EDGE component and a cloud-based SaaS management cockpit.
The EDGE component of ORBIS DSP is the local instance for the standardized connection of production machines. All administration related to locally used services takes place in the cloud-based management cockpit, such as organization mapping (plants and machines/systems installed there) and the configuration of data and process flows. The cockpit therefore regulates which data flows into which applications and processes, whether in Waldkraiburg, the US or Asia.
Entry into digital, paperless production
Six machines, which are used to manufacture pump stators, are currently connected to the interoperable and scalable shop floor platform. It has helped to optimize and significantly shorten order processing and make production control noticeably more efficient. This has in part been possible because ORBIS MES interacts perfectly with ORBIS DSP and SAP S/4HANA to reliably guide workers through their tasks with dialog support. The platform also enables the reporting of key production figures at product, machine, and location level. All processes can be carried out digitally from start to finish, in other words without manual intermediate steps and therefore without system and media disruptions.
In practice this works as follows: The parameters for the machines used to manufacture the pump stators are maintained and stored in the Microsoft Power app. Depending on the production material, the specifications/conditions that a machine has to adhere to, for example in terms of its horizontal and vertical position, pressure or temperature, are defined so that the production process can start. When the values meet the specifications, the worker gives the go-ahead in the app and the parameter sets are transferred to the EDGE component of ORBIS DSP.
The relevant production orders are created in SAP S/4HANA. The EDGE component links the production order in SAP with the corresponding parameter sets, which are loaded from the cloud and triggers the setup of the machine. As soon as this process is complete, a confirmation is sent to the MES, which starts production via the EDGE component. When a machine indicates that production is complete, this information is transmitted to SAP S/4HANA via the EDGE component and the MES, and the production order is completed there.
But that isn’t all. The downstream inspection of the stators in an inspection room, carried out on the basis of inspection lots, is also processed via ORBIS DSP. The solution captures the measurement results and transfers them to the actual value fields of the relevant inspection criteria, which are stored in the SAP inspection lot.
Process data analysis in Power BI
The process data generated by the machines on set-up and production times, as well as production parameters such as pressure, temperature and speed, flow into the Azure IoT platform via the EDGE component. They are stored there and evaluated in detail using the Power BI analysis tool. This enables efficient reporting of key figures, which can provide information on optimization potential in Production e.g. in terms of set-up times. In addition, the stored process data and production parameters can be used to seamlessly track the entire production process of a stator. This traceability is an important aspect as far as product liability is concerned and an essential part of quality management.
Implementation with an established IT partner
ORBIS SE was tasked with implementing the new shop floor platform, having already carried out several SAP projects at NETZSCH, including the system conversion to SAP S/4HANA. The international IT service provider has extensive expertise in shop floor solutions and offers a portfolio ranging from EDGE and ORBIS MES to Power Platform, Azure IoT and Power BI.
Thanks to the close collaboration between the project teams at ORBIS and NETZSCH, the complex project was completed as quickly as possible. The development of the Power app for creating, storing, and maintaining parameters for production specifications and the transfer of a large amount of stator-related legacy data, process data and measurement values in various formats, and their harmonization, presented particular challenges.
ORBIS experts used the Azure Data Factory data integration service to handle this. ORBIS was also tasked with redesigning and implementing the entire material flow in SAP for the new production hall in Waldkraiburg, which houses an assembly plant and a fully automated high-bay warehouse for pump components. This included everything from connecting automatic pallet and small parts storage systems to supplying Production with tugger trains.
Andreas Freiberger is pleased with what has been achieved so far,
“We are combining SAP and ORBIS solutions as well as Azure-based cloud applications to create a modern, hybrid platform for digital shop floor management. ORBIS DSP is an integral part of this, ensuring the interoperability of individual applications and choreographing data flows.”
Andreas Freiberger, SAP Inhouse Consultant at NETZSCH
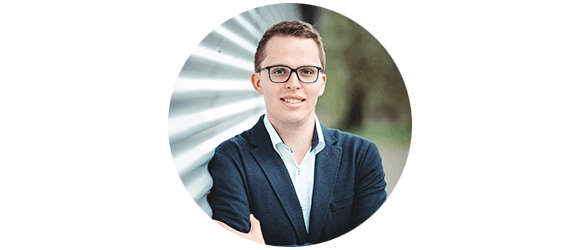
But this is just the beginning: a further six machines are set to be gradually connected to the platform, which is constantly being improved and developed further. There are also plans to roll it out to other locations, including at international sites; it has already been launched at a new plant in Asia.